BOC Smootharc TIG 185 DC Instrukcja serwisowa - Strona 16
Przeglądaj online lub pobierz pdf Instrukcja serwisowa dla System spawania BOC Smootharc TIG 185 DC. BOC Smootharc TIG 185 DC 19 stron. Boc smootharc tig 185 dc welder
Również dla BOC Smootharc TIG 185 DC: Instrukcja obsługi (15 strony)
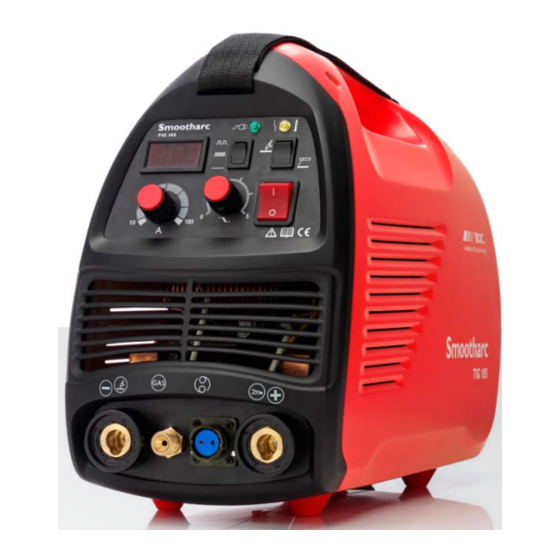
16
BOC Smootharc TIG 185 DC Service manual
2.0 T roubleshooting and maintenance
Problem
1 P ress the power switch,
power indicator, meter, and
fans with no data, press the
torch without response.
2 P ress the power switch, the
power indicator and meter is
ok, the fan is abnormal, the
machine has no response
when pressing the switch.
3 P ress the power switch,
power indicator, meter, and
fan works normally. Press the
switch of the torch without
response.
4 T urn on the machine
normally, without high
frequency
5 T urn on the machine
normally, the abnormal
indicator is on.
6 T urn on the machine
normally, could start arc, but
the weld appears black.
7 T he welding current is
unstable, uncontrollable.
8 S kip after turning on the
machine.
9 T he high frequency could not
stop.
Possible Reasons
1 C heck the circuit is normal, and external power supply (AC240) is OK.
2 C heck the power cable, switch, and connector is tightly connected, use a multi-meter
to test the plug (PZ01-005-O1 CON10) for DC340V±5V.
1 C heck the inverter board has DC24V output, use a multi-meter to test the CON4's
PM01-001-E12 pin 1 and 2. If it has 24V output, test other areas.
2 S tart relay K1 on bottom board does not respond properly (it can be indicated by the
solenoid valve jumping).
3 S tart relay K2 in power circuit does not respond properly, check optical U1, MOSFET
Z24 (Q4) resistor RV1, and whether the relay is damaged or not.
4 P ressing the power button continuously in a short time, results in the field-discharge
resistance becoming overheated P ower off the machine for several minutes.
1 S witch of the torch or the cable is loose.
2 Gas socket is loose or the cable is broken.
1 P ull off the high frequency cable(PM01-001-E12 CON2), use a multi-meter to test
the output for DC230. If yes and could start arc, check the starting arc under high
frequency.
a) C heck whether the high frequency cable connection to the bottom board
(PZ01-005-O1 CON4) and cable for arc start is not loose.
b) C heck if the high voltage discharge nozzle is connected correctly, or the surface is
oxidized.
c) C heck if the high voltage components (D3-D6), high voltage output capacitors
(C7, C10, C11) are not damaged.
d) C heck the high frequency relay on the bottom board is responding properly.
2 C heck for the DC230 output, possibly the inverter circuit is abnormal.
a) C heck if the control module, has output for the drive signal or works normally.
b) C heck if the inverter and main current cable is not loose PM01-001-E12 CON1 .
1 T he over-heat protection is activated, turn off the machine, and could restart the
machine successfully while the power indicator is off.
2 T he over-heat protection works, the machine will be ok after 2-3 minutes.
3 T he inverter circuit and start arc is abnormal, turn off the machine and pull off
the plug of the high frequency start arc power in PM01-001-E12, then turn on the
machine and press the switch.
a) I f the abnormal indicator does not go on, the transformer T1 on the PZ01-005-O1
or D3-D6 is damaged.
b) I f the abnormal indicator is on, then pull off the plug CON1 for power supply
in the PM01-001-E12 If the light is still on, some of the MOSFET components
are damaged. If the light goes off, the rectifier pipe on PZ01-005-O1 or the
transformer is damaged.
c) C heck if the feedback circuit is open-circuit, check the feedback cable is properly
connected.
1 C heck if the solenoid valve is jammed or damaged.
2 T he solenoid valve relay (PZ01-005-W K1) is damaged.
3 C heck the torch for wear or damage.
4 T ungsten electrode is in poor condition, or the shielding gas is incorrect.
1 T he potentiometer is loose or damaged.
2 F iltering capacitor PZ01-005-O1 in the bottom board is leaking or damaged.
3 T he welding cable is too long and thin resulting in the unstable current.
1 T he rectifier silicon bridge is damaged.
2 T he power cable is short-circuited.
1 H igh frequency relay (PZ01-005-W K3) is damaged.
2 T he output voltage disturbs the voltage.
Ver.1 Rev.1 . 0314
Solution
1 C heck the external power
supply.
2 C heck the connector.
1 C heck and remove.
2 C heck and remove.
3 C heck and remove.
4 T urn off the machine for
several minutes.
1 C heck and remove.
2 C heck and remove.
1 C heck and replace.
2 C heck and replace.
1 T he machine will be ok after
turning off the machine for
five minutes.
2 S top the machine for a while.
3 C heck and remove.
1 C lean.
2 C heck and replace if
necessary.
3 C heck and replace if
necessary.
4 R eplace.
1 C heck and remove.
2 C heck and remove.
3 I ncrease the cross section of
the cable.
1 C heck and replace.
2 R eplace.
1 C heck and remove.
2 A dd capacitor between
output and ground.