Dynamatic 15-533-1015 Инструктивный лист - Страница 11
Просмотреть онлайн или скачать pdf Инструктивный лист для Контроллер Dynamatic 15-533-1015. Dynamatic 15-533-1015 14 страниц.
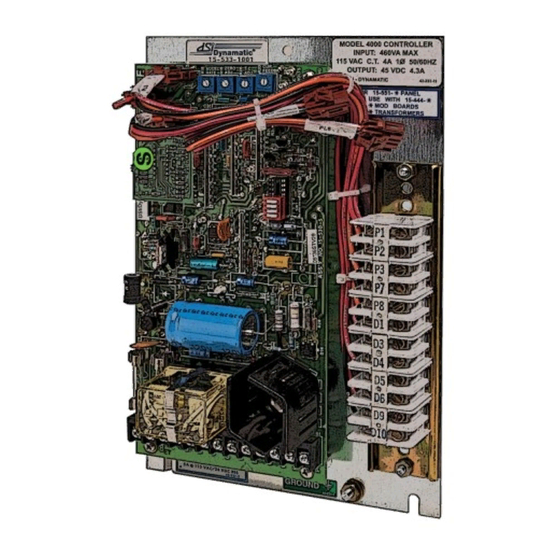
8.
Accel Rate R18-
The purpose of Linear Acceleration is to slow down drive response to an increase
in command. Without Linear Accel control, the drive will respond to operator speed adjustments
very quickly, limited only by the torque capacity of the drive. With the Linear Accel circuit, the
output of the controller is linear with respect to time. This circuit is adjustable from 3 to 90
seconds. When set at the slowest acceleration rate, the drive will take 90 seconds to accelerate
from zero to rated speed, following a linear ramp. When less than rated speed is set, this time
required to reach top speed is proportionally less.
The Linear Acceleration circuit may be activated or deactivated in both Manual/Run and
Jog/Thread/Auto modes by setting the programing switches as indicated on the programming
chart on the connection diagram.
To set the Accel Rate: stop the controller with the Stop pushbutton. Turn the Run Speed
potentiometer to 100% (Full CW). With the drive at a complete stop, push the Start pushbutton,
and time the interval required for the drive to accelerate from zero to full speed. Adjust the Accel
Rate potentiometer R18, accordingly, CW for a faster accel rate.
9.
Velocity Damping R22*-
response (drive response is a function of the clutch coil time constant and system inertia). The
proper setting for this adjustment depends upon the drive size and total inertia.
See Preliminary Adjustments. If instability (speed control becomes erratic) occurs at any setting
increase (turn CW) slightly until the speed becomes stable.
*See basic 4000/4050 manual for a more destined description of this adjustment.
HI Damping R20-
10.
applications, such as stamping presses, where the load inertia is greater than 5 to 10 times the
drive inertia. In these cases, turn the Velocity Damping pot R22 on the main board to zero (full
CCW). Now adjust the HI Damping pot R20 the modification board until the proper response is
achieved (neither oscillatory nor sluggish). If, however, maximum CW is attained and the system
remains oscillatory, further damping may be obtained from R22 on the main board. The main PCB
Velocity Damping pot R22 has about 75% of the damping range that the HI Damping pot R20 has
on the modification board. However, they may be used in combination on high inertia applications
where increased damping is required.
11.
Torque Limit PCB 15-444-2
a. Apply a normal load on the mechanical unit driven by the clutch
b. Monitor the motor current. Since current is proportional to torque check your nameplate for
the rated motor current to determine the desired torque limit. Example- if your drive is rated
at 10 amps, and you want to limit the torque (150% of 10 amperes is 15 amperes), start the
drive and note the maximum current on the ac ammeter during acceleration. If the current
tis less than a50% of rated motor torque, increase the Torque Limit setting R19 CW. If the
current rating is too high, decrease the Torque Limit setting CCW. Stop the unit and repeat
the Start Up. Check on the ac ammeter during acceleration. If the motor current during
acceleration never reaches 150% of rated motor current, Increase the load and repeat current
monitoring.
11
this potentiometer is used to match the controller response to the drive
This pot is located on the Torque Limit modification board. It is used for
(Normal Load)